Schedule a Call Back
Design-build is best suited for the affordable housing programme
2019-04-01
Given land prices and other constraints in the urban areas and metropolitan cities of India, building high-rise residential towers for affordable housing becomes imperative. SC Dixit, Executive Director, Shapoorji Pallonji Engineering & Construction, shares more on technologies that can be adopted to meet the dire need of faster construction for affordable homes, in conversation with SERAPHINA D?SOUZA.
You have been awarded affordable housing projects in Andhra Pradesh. What is the average time currently taken for development per sq ft and at what cost?
We have been awarded EPC contracts by the Andhra Pradesh Township Infrastructure Development Corporation (APTIDCO) for delivering a total of about 144,300 EWS dwelling units at various locations in Andhra Pradesh, spread over the districts of Guntur, Kurnool, Nandyal, Ananthapur, West Godavari and Prakasam. The total built-up area involved in the construction of these EWS units is to the tune of 50 million sq ft and the value of these works adds up to about Rs 84 billion. In addition, we have also been awarded the EPC contract by the Andhra Pradesh Capital Region Development Authority (APCRDA) for the construction of 1,440 housing units for gazetted officers at Andhra Pradesh Government Complex in the new capital region. The built-up area of this project is about 2.7 million sq ft and the contract is valued at about Rs 7 billion. Works are on in full swing; all these contracts need to be delivered phase-wise between March 2019 and March 2020. The average time period for delivering each phase is about 18 months.
What are your requirements for constructing houses in a shorter period of time that will lead to faster delivery of projects?
Generally speaking, the factors that can expedite the construction of affordable housing projects are:
- Freezing of user requirements that ensures architectural, structural and MEP design readiness.
- Faster approval process to be adopted for architectural, structural and MEP designs by the decision-makers.
- Adoption of advanced technologies such as monolithic concrete construction (shear wall technology) using aluminium formwork or precast construction. These technologies reduce cycle times and the requirement of construction labour, reduce project duration vis-?-vis conventional construction, reduce material wastage, and improve construction quality and safety. These technologies also eliminate labour-intensive activities such as masonry and plastering, thus leading to time and cost savings.
- No design changes to be introduced during the construction process. This affects the progress of construction work.
- A high degree of modularity of designs that ensures a higher repetition of formwork and higher productivity of mobilised resources.
- Other contributing factors include:
- Site readiness free from all encumbrances and clear work-fronts for all activities.
- Availability of all building permits and sanctions prior to commencement of construction.
- Availability of funds with the developers or project promoters to ensure smooth cashflows and work progress.

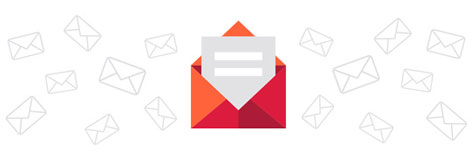
Subscribe Now
Subscribe to our Newsletter & Stay updated
RECENT POSTS
Popular Tags
Folliow us
Related Stories
Rs 13.10 Bn Desalination Plant Cleared for Kakinada SEZ
Kakinada SEZ Limited, a wholly owned subsidiary of Auro Infra Realty and Infrastructure, is set to construct a 3x50 MLD desalination plant in Kon...
Rajasthan Becomes Leading Hub for Decentralized Solar Power
Rajasthan is quickly emerging as a leading centre for decentralized solar energy in India, complementing its broader progress in the solar power ...
Chennai Metro to Install Real-Time Info Boards Across City
Chennai Metro Rail Limited (CMRL) has initiated a project to install digital display boards at key public locations to guide commuters using real...