Schedule a Call Back
Tenders should mandate at least 30-40% use of precast or prefab components
2019-04-01

- MV Satish, Whole-Time Director & Senior Executive Vice-President (Buildings, Minerals & Metals), Larsen & Toubro
With the aim to construct 1.2 crore homes to ensure Housing for All by 2022, the Pradhan Mantri Awas Yojana-Urban (PMAY-U) calls for out-of-the-box, innovative thinking. And so, the government has launched the Global Housing Technology Challenge (GHTC) to look for new, emerging, disaster-resilient, environment-friendly, cost-effective and speedy construction technologies. ?As it is important to bring in a technology transition to avail of the best technologies globally, GHTC will help bridge the demand-supply gap in the affordable housing sector,? says MV Satish, Whole-Time Director & Senior Executive Vice President (Buildings, Minerals & Metals), Larsen & Toubro (L&T). In this segment, the company is constructing about 89,300 flats or apartments of varying sizes ? 300 sq ft, 365 sq ft and 435 sq ft over a total built-up area of 31 million sq ft ? across several districts in Andhra Pradesh. L&T is also actively looking at a few emerging technologies to hasten this process, adds Satish, as he shares his thoughts on the affordable housing segment with SERAPHINA D?SOUZA.
What is the average time currently taken for per square feet development of affordable housing units?
Aluminium formwork is one of the construction methods being increasingly used to reduce execution time and costs. Time taken using aluminium formwork is not measured in square feet completed but in time taken to cast floor slabs. This is called cycle time, which includes the time to set up the formwork for casting, tying reinforcement, pouring concrete, concrete setting and removal of formwork. At present, we are executing residential projects at a rate of seven days per floor slab for RCC works. All these jobs have stringent delivery schedules of
15 months.
What are your requirements in terms of technologies for constructing houses in a shorter period of time for faster project delivery?
L&T has been at the forefront of adopting frontier technologies, having been first to introduce tunnel formwork and aluminium system formwork in India, in residential construction, over a decade and a half ago. With these, an entire floor slab can be cast monolithically to significantly decrease execution time. There is definitely a need to mechanise construction activities offsite to reduce construction time, but that will be affordable only when the volume of construction
is high.While various technologies are available from across the globe to quicken the pace of construction, the need for a more enabling environment is critical, in which technology transfer and adoption can be easier.
Specific focus is now on prefabricated construction, where not only is the structural system precast but the overall building finishing and MEP works completed in a factory, with the finished units being assembled at site. A similar approach has recently been adopted by the Singapore Government, which has mandated the use of precast prefabricated volumetric construction (PPVC) for finished kitchens, bedrooms and bathroom units.
With reference to government-funded projects, the first requirement is for tenders to be based on technology, rather than leaving them technology-neutral. This will create a level playing field for contractors who are willing and capable of adopting superior technologies without being outpriced in the bidding process.
At the same time, prequalification criteria need to be relaxed to promote new technologies.
Tenders should mandate at least 30-40 per cent use of precast or prefab structural components.
The government should sponsor or subsidise research programmes of technology providers and offer incentives to contractors to adopt new technologies. From the perspective of the Bureau of Indian Standards (BIS), there is a need to customise codal requirements for affordable housing to reduce material consumption (which is a major contributor to increasing construction costs) and for the adoption of international standards in the absence of equivalent Indian codes or their extremely old versions. Even from an architectural standpoint, it is imperative to lay down standard specifications for modular units, their dimensions, for doors, windows and the like, to enable modular construction.
Are there any global technologies India should adopt to hasten the construction of affordable housing?
The precast large concrete panel system is widely regarded as a technology to hasten construction of affordable housing. Globally, the precast construction market is expected to reach $185.23 billion by 2022 at a CAGR of 6.3 per cent according to Allied Market Research. This technology has already been well accepted and adopted in the Middle East, Southeast Asia, China and Europe. It is being introduced in India, too, and we foresee its widespread use in the country soon.

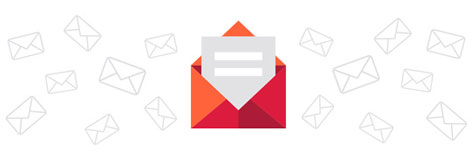
Subscribe Now
Subscribe to our Newsletter & Stay updated
RECENT POSTS
Popular Tags
Folliow us
Related Stories
Rs 13.10 Bn Desalination Plant Cleared for Kakinada SEZ
Kakinada SEZ Limited, a wholly owned subsidiary of Auro Infra Realty and Infrastructure, is set to construct a 3x50 MLD desalination plant in Kon...
Rajasthan Becomes Leading Hub for Decentralized Solar Power
Rajasthan is quickly emerging as a leading centre for decentralized solar energy in India, complementing its broader progress in the solar power ...
Chennai Metro to Install Real-Time Info Boards Across City
Chennai Metro Rail Limited (CMRL) has initiated a project to install digital display boards at key public locations to guide commuters using real...