Schedule a Call Back
Overcoming Perceptions and Scaling Up
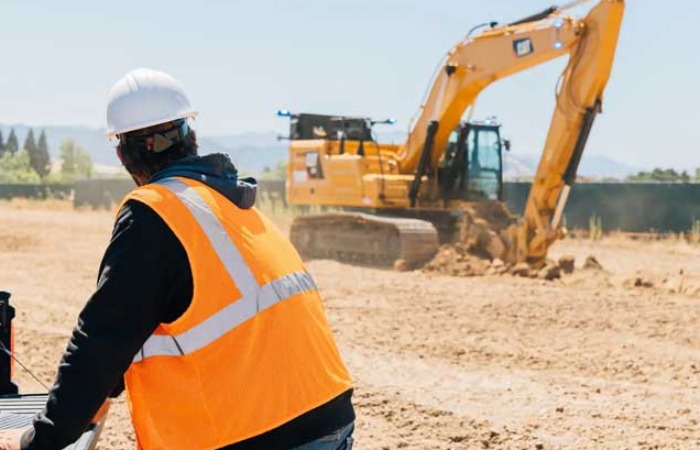
India’s manufacturing and construction equipment industries are at a pivotal juncture. With rapidly evolving infrastructure needs and increasing global demand, the sector stands poised for substantial growth. However, to meet the ambitious goals set for the next decade, it must address several challenges, from improving product quality and technological innovation to fostering international collaborations. The country’s strategy for growth in these industries is multi-faceted, focusing on not just scaling up production but enhancing supply chain efficiencies, overcoming global perception challenges, and investing in research and development (R&D).
Growing demand,
a challenge
India is currently the third-largest player in the global construction equipment market, but with a contribution of only 5 to 6 per cent of the $150 billion global market, it has significant room for growth. The domestic market, however, is on a rapid upward trajectory. According to Sunil Kumar Dixit, President, Manufacturing Operations, Schwing Stetter India, India’s construction equipment industry must double its size by 2030, with equipment demand rising from around 1,25,000 pieces annually to a potential 3,00,000. The drive for modernisation, infrastructure development, smart cities, and sanitation projects is fuelling this demand, making India a key player in the future of the construction equipment sector.
India’s growing position as a manufacturing hub is being further strengthened by the “China+1” strategy, where countries are actively seeking alternatives to China for their manufacturing needs. India, with its cost-effective labour and expanding industrial capabilities, is emerging as the first choice for many nations. Yet, challenges remain. Smaller countries like Vietnam have managed to build a more specialised workforce with sector-specific skills. India's push to improve through collaborations between industry, academia, and government is crucial to competing globally.
Despite these hurdles, the opportunity to shift from being a mere fabrication hub to a leader in component manufacturing is within reach. Dixit emphasises the importance of investing in R&D. India’s future success hinges not only on scaling up manufacturing but also on creating products that meet international standards, including those in emissions and sustainability.
Overcoming
global perceptions
One of the most significant barriers India faces in the global market is the perception of its products. Historically, Indian manufacturing has been associated with low-cost options, often perceived as inferior in quality. To compete with established brands from Germany, Japan, and the US, India must shift this mindset.
Sanjeev Bajaj, CEO, Escorts Kubota, highlights the need to address this perception, especially when it comes to the construction equipment industry. “We need to change the mindset of customers who may view Indian products as low-cost alternatives,” he says. While India’s products may not yet match the quality of German or Japanese counterparts, the gap is closing. The challenge now is to move faster in improving quality and meeting global standards.
A Rajesh Premchandran, Marketing Officer, NBC Bearings, which supplies critical components like bearings to global markets, echoes this sentiment. “Ensuring quality is non-negotiable,” he says, explaining that small components like bearings have a large impact on the overall performance of machinery. He underscores that consistent quality across markets—from India to the US—is vital for maintaining global competitiveness.
Meanwhile, companies like CEAT Specialty have already shown that Indian products can not only compete but surpass international standards. Dyutiman Chattopadhyay, Vice President, Research, Development & Technology, CEAT Specialty, shares that their Indian-manufactured tyres have captured significant market shares in countries like Australia and the US. He believes that Indian products are now on par with European brands, if not better, emphasising that cost competitiveness does not come at the expense of quality. This success story is a testament to the industry's growing global credibility.
Leveraging
Make in India
The “Make in India” initiative has given Indian manufacturers an edge, especially in sectors like engines and emission technologies. Samir Kale, Senior General Manager, Kirloskar Oil Engines, explains that the initiative has been pivotal in driving localisation, particularly in the commercial vehicle sector, which has seen significant improvements in engine technologies and emission standards. The government’s push towards sustainability and greener technologies is providing further opportunities, particularly with stricter emission standards worldwide.
However, the challenge remains to shift the global perception of Indian products. While Indian companies are now meeting global standards in areas like emissions, many international markets still hesitate to fully embrace Indian products. To address this, the sector must continue investing in R&D and innovation. Dixit advocates for a more robust focus on R&D within India, not just for fabrication but also for developing proprietary technologies that meet Indian and international standards. By doing so, India can carve out a significant place in the global market, not merely as an assembly hub, but as a leader in technological innovation.
A strong and sustainable manufacturing ecosystem requires continuous innovation, which in turn demands an equally robust talent pool. The government and industry must collaborate to foster the next generation of engineers and technologists. Premchandran points out that a major challenge India faces is retaining young talent, particularly as many graduates prefer to work in the digital space rather than the traditional manufacturing sector. To attract and retain talent, the industry must evolve to offer more innovative and engaging work environments, incorporating automation and AI to make manufacturing more appealing.
Kale also emphasises the need for deeper industry-academia collaboration. If academic institutions like IITs and IIMs can align their curriculums with the evolving needs of the manufacturing sector, it will help bridge the skill gap and fuel the next wave of innovation. Public-private partnerships in R&D and education could create a more dynamic, skilled workforce ready to meet both domestic and global demands.
Finally, government support remains crucial to ensuring the sector’s competitiveness. Samir Kale suggests that further incentives for R&D investment would go a long way in advancing the sector. Additionally, fostering more free trade agreements (FTAs) would open up new markets and increase India’s global competitiveness. Political stability, consistency in policies, and access to funding for high-tech innovation are all critical factors in ensuring that India remains at the forefront of global manufacturing.
The road ahead
India’s construction and manufacturing sectors stand
on the brink of significant transformation. With a combination of strategic
planning, technological investment, and international collaborations, the
country has the potential to lead the global market in the next decade. The
challenge will be to move beyond the perception of India as merely a
cost-effective hub to one recognised for its high-quality, innovative, and
sustainable products. By addressing these challenges head-on, India can secure
its place as a global manufacturing leader, contributing not just to its own
growth but to the future of industries worldwide.

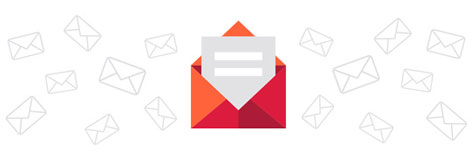
Subscribe Now
Subscribe to our Newsletter & Stay updated
RECENT POSTS
Popular Tags
Folliow us
Related Stories
We are expanding our portfolio from 1,000 to 3,000 SKUs
Could you start by telling us about your recent product launches and what you are displaying at bauma Conexpo 2024?
We are a fully “Made in India” company
Tell us about your company and its major products.