Schedule a Call Back
Future Excavated
2025-05-27
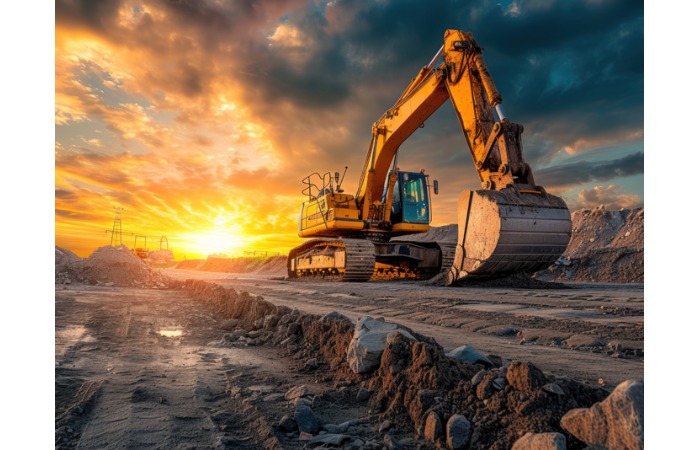
In India’s sweeping infrastructure transformation, hydraulic excavators have emerged as the silent powerhouses behind the scenes. Whether it’s tunnelling through rocky terrain for metro lines, preparing the earth for highways, or undertaking mining and irrigation projects, these machines are redefining how India builds. But the evolution isn’t just in their scale or strength—it’s in their intelligence, sustainability, and versatility.
Once seen as simple dig-and-dump machines, hydraulic excavators today are smart, fuel-efficient, and connected. They are evolving alongside the nation's ambitious goals: a $1.4 trillion infrastructure pipeline under the National Infrastructure Plan, annual construction of over 12,000 km of national highways, and a growing number of smart cities and urban transit systems. In this ambitious context, the excavator is becoming not just a piece of equipment, but a strategic asset.
Growing market
India’s hydraulic excavator market is currently estimated to be worth around Rs 12,000 crore. But numbers alone don’t tell the full story. What’s significant is the expected leap in the number of machines on the ground—from approximately 90,000 units today to a projected 2,50,000 units by 2030. That’s nearly a threefold increase in just over five years.
This surge is being fuelled by multiple segments—urban infrastructure, mining, roads, and irrigation—all of which have unique demands. Urban projects lean toward compact models due to tight spaces and regulatory norms, while road-building and mining demand heavier, high-performance machines. Add to this the expanding role of rentals and organised leasing, and the market begins to look both broad and complex.
The OEM race
The Indian excavator landscape is currently a highly competitive space with leading players such as Tata Hitachi, Volvo CE, Komatsu, L&T Komatsu, XCMG, and Gainwell with Caterpillar each pushing technological and operational boundaries.
Tata Hitachi has focused on the urban and semi-urban market with its ZAXIS 38U, a mini zero tail swing excavator, and the SHINRAI Prime backhoe loader. Designed for confined workspaces in cities, these machines boast better fuel efficiency and more operator comfort than previous models. The ZAXIS 38U, in particular, shines in applications such as trenching, landscaping, and foundation work, where precision and mobility are crucial.
Meanwhile, Volvo Construction Equipment has set a new benchmark with its EC210-A, an upgraded version of its popular EC210D model. The new excavator comes with a smart hydraulic system that improves fuel efficiency without compromising digging power. The integration of Volvo’s CareTrack telematics system allows real-time monitoring of machine performance, predictive maintenance, and remote diagnostics—features that are particularly valued in remote infrastructure sites. “Contractors need reliable, fuel-efficient machines that also support sustainability goals. Our EC210-A is designed with that in mind,” said Dimitrov Krishnan, Managing Director, Volvo CE India.
Komatsu, through its joint venture with L&T, is banking on automation and machine control. Its PC220LCi-12, recently unveiled in India, comes with the company’s proprietary Intelligent Machine Control (iMC), which automates grading and digging operations, drastically reducing errors and improving productivity. On the compact side, L&T Komatsu’s new mini hydraulic excavator offers flexibility and ease of use for small contractors working in congested job sites—a growing niche as urban projects pick up steam.
Gainwell, Caterpillar’s dealer in India, brought attention to its electrohydraulic excavators and the RM500 Reclaimer at bauma Conexpo India 2024. The electrohydraulic systems replace traditional pilot lines with digital actuators, which increases fuel efficiency and enables more accurate operation. “These machines bring unmatched productivity while significantly lowering emissions and fuel usage. It’s a win-win for contractors and for India’s sustainability goals.”
Chinese major XCMG isn’t far behind. At bauma China 2024, it unveiled an impressive lineup of 17 new excavator models. These machines, several of which are expected to make their way to India, are designed with advanced engine technology, multi-functional work modes, and superior operator comfort. They also incorporate IoT-enabled systems for monitoring and control, underlining how even budget-sensitive markets like India are demanding higher intelligence from their equipment.
HD Hyundai Construction Equipment India has taken a firm step forward with a strong focus on mining and exports. According to Sharwan Agnihotri, Head – Mining & Export Business, HD Hyundai Construction Equipment India, “We are increasing our mining portfolio and expanding in exports. Hyundai machines are known for their reliability, technology and performance. We are enhancing our capacity in India to support both domestic demand and overseas markets.” Hyundai’s offerings in the mining segment aim to deliver durability and productivity under harsh working conditions—key needs for India’s expanding surface mining and quarrying operations.
Trends defining the next-gen excavator
The Indian hydraulic excavator is undergoing a transformation that mirrors global trends, though shaped by local constraints and opportunities. Five major developments are leading this evolution:
Electrohydraulics is one of the most notable shifts. Machines like Caterpillar’s new excavators use electric actuators instead of hydraulic pilot controls, allowing for more precise operations and reducing energy loss. This not only improves fuel economy but also results in smoother operation, particularly important for fine tasks like grading and trenching.
Telematics and remote monitoring are now standard in machines from major OEMs. Systems such as Komtrax (from Komatsu), VisionLink (Caterpillar), and CareTrack (Volvo) provide real-time data on machine health, fuel use, idle time, and location. This facilitates predictive maintenance and improves machine uptime—vital in large projects where equipment failure can delay work and increase costs.
Automation and intelligent machine control (iMC) are also making inroads. Komatsu’s iMC 2.0, for example, enables semi-automatic operation by allowing the excavator to adjust its position and operation based on jobsite parameters. These systems reduce the dependence on highly skilled operators, improve accuracy, and cut rework.
Environmental responsibility is becoming a key concern, not just for OEMs but also for contractors bidding on government projects with sustainability clauses. While electric excavators are still in their infancy in India, hybrid and low-emission diesel models are gaining traction. Volvo, Tata Hitachi, and XCMG are reportedly testing battery-electric variants in controlled settings.
Operator comfort and safety have become central design elements. New machines now feature ergonomic seats, touchscreen controls, panoramic visibility, climate control, and noise-reduction cabins. With a growing emphasis on operator welfare and productivity, these upgrades are no longer optional extras—they are baseline expectations.
Challenges on the ground
Despite the technological advances, several structural challenges remain. First, the cost of advanced machines remains high, mainly due to the import of precision components and electronic systems. While demand is strong, price sensitivity in India forces OEMs to strike a delicate balance between innovation and affordability.
Second, there is a shortage of trained operators who can handle these modern machines. Many OEMs, including Tata Hitachi and Komatsu, have responded by establishing training centres and offering simulator-based programs. Still, upskilling the workforce to match equipment sophistication remains a slow process.
Third, the after-sales service network in tier-2 and tier-3 cities is still underdeveloped. Though some OEMs have begun rolling out mobile service vans and remote diagnostic platforms, the availability of spare parts and skilled technicians remains uneven.
Lastly, the construction equipment rental market, while growing rapidly, is still fragmented. Organised rental platforms like Mycrane, Infra Bazaar, and RentHire are attempting to bring transparency and efficiency, offering contractors access to newer machines without large capital investments. However, regulatory support and industry standardisation are still evolving.
The road ahead
Looking ahead, the hydraulic excavator is poised to become more than just a machine. It will be an intelligent partner on the construction site—capable of learning, adapting, and optimising operations in real time.
India’s infrastructure ambitions demand machines that can build faster, smarter, and greener. By 2030, it’s not unreasonable to imagine excavators that self-adjust to soil conditions, interact with Building Information Modelling (BIM) software, run on clean energy, and automatically order parts or schedule service calls.
The excavator of tomorrow isn’t just about digging. It’s about doing more with less—less fuel, less time, less error. That’s the future India needs, and that’s the future we’re building towards.
India’s hydraulic excavator market is at an inflection point. From being rugged tools of brute force, excavators are morphing into smart, sustainable, and scalable enablers of infrastructure growth. OEMs, users, and regulators must now align to create an ecosystem that nurtures this transformation—through better policies, training, and collaboration. If that happens, the humble excavator might just become the symbol of India’s next developmental leap.

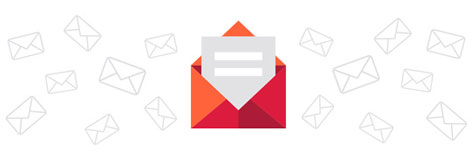
Subscribe Now
Subscribe to our Newsletter & Stay updated
RECENT POSTS
Popular Tags
Folliow us
Related Stories
“Our cutting-edge excavators are Made in India.”
How are hydraulic excavators used in different construction and mining applications?
With India investing heavily in roads, rail...
Read More
“Our cutting-edge excavators are Made in India.”
How are hydraulic excavators used in different construction and mining applications?
With India investing heavily in roads, rail...
Read More
Cost Optimisation for Building Durable Roads
Road construction plays a vital role in infrastructure development, serving as a catalyst for economic growth, improved regional connectivity, and ...