Schedule a Call Back
Cost Optimisation for Building Durable Roads
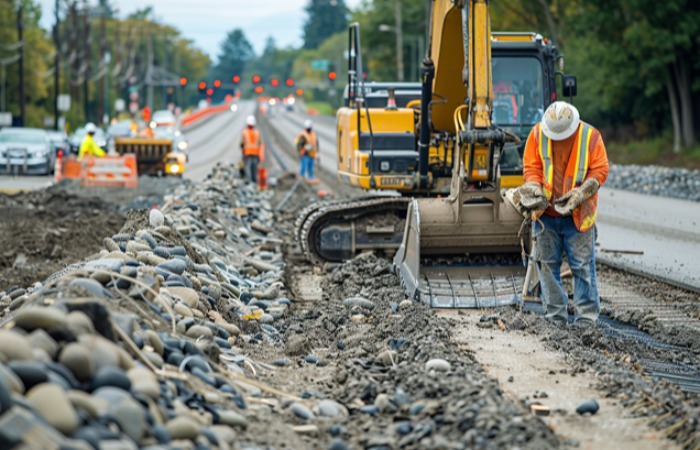
Road construction plays a vital role in infrastructure development, serving as a catalyst for economic growth, improved regional connectivity, and urban development. Since April 2014, India has constructed and upgraded nearly 101,900 km of National Highways (NH). The average annual rate of highway construction from 2014 to 2024 has surged by approximately 130 per cent compared to the 2004–2014 decade. Looking ahead, the Union Government has set a bold goal of building 10,000 km of highways in the 2025–26 fiscal year.
However, despite this rapid expansion, challenges such as budget overruns, project delays, and environmental impacts continue to affect the efficiency and sustainability of road infrastructure projects. Achieving cost efficiency in this sector requires a careful balance between maintaining quality, adhering to timelines, and staying within budget, all while minimising environmental impact. Contributing factors to rising costs often include inadequate project planning, limited adoption of advanced technologies, and poor resource management. Additionally, while striving to meet global quality standards is crucial, it must be done without compromising financial discipline.
Hence, there is a need to explore ways to reduce costs across the road construction lifecycle—starting from planning and design to material usage, execution, and long-term maintenance—without compromising on the quality or performance of infrastructure.
Early-stage planning: The hidden lever
According to R K Pandey, former Member (Projects), National Highways Authority of India (NHAI), cost overruns often originate during the planning phase. "Planning and pre-construction activities are the two foundations for successful completion of a project. Alignment selection, land acquisition, and detailed project reports (DPRs) must be approached with cost, environmental, and lifecycle considerations in mind,” he stresses.
The shift from brownfield to greenfield alignments, as adopted under the Bharatmala programme, exemplifies this strategic mindset. While initial costs may be higher, greenfield projects offer shorter routes, reduced congestion, and lower lifecycle maintenance costs. Similarly, elevated corridors, as opposed to constructing multiple bypasses, could be a long-term solution to land scarcity and urban sprawl.
Highlighting the importance of vertical alignment choices and the need to reassess standard practices such as paved shoulder design, Pandey says, “If paved shoulders are not subjected to the same level of traffic, why must they match the carriageway in design? These are areas where rethinking standards can lead to meaningful cost savings.”
Many experts emphasis that cost optimisation must be approached not as cost-cutting, but as intelligent engineering. “There's a fine line between reducing costs and compromising safety. We need industry and policy-level mechanisms to ensure innovations in materials and methods are implemented meaningfully,” explains Dr V Ramachandra, Director, RASTA – Centre for Road Technology.
He points out that while the Indian Roads Congress (IRC) accredits new technologies and materials, implementation remains inconsistent. A structured framework for pilot projects, followed by feedback loops and refinement of standards, is essential. “For example, alternative aggregates have been approved, but unless we monitor their field performance, the industry will remain cautious,” he adds.
Dr Ramachandra also suggests incorporation of lifecycle cost analysis in tender evaluations rather than relying solely on initial construction costs. “This shift would naturally promote the adoption of durable and sustainable methods over cheaper, short-term solutions,” he opines.
The role of independent quality audits
Ensuring quality through third-party quality audits is also essential for building durable roads. Explaining the value of such assessments, Dr Manoranjan Parida, Director, CSIR-Central Road Research Institute (CRRI), says, “Third-party audits are akin to safety assessments conducted for metro or railway projects before opening to the public. They ensure compliance and help identify construction lapses early.”
He advocates for concurrent audits, conducted during construction instead of post-completion, to enable timely interventions and reduce rework-related costs. “Early detection of defects leads to significant savings, while enhancing durability and safety of the finished road,” he stresses.
This, according to Dr Parida, is particularly important in high-value projects involving multiple agencies, where accountability and coordination can sometimes fall through the cracks.
Private sector perspective: Optimising under constraints
As a long-time champion of Public-Private Partnership (PPP) models, Dr Sudhir Hoshing, Chief Mentor at IRB Infrastructure Developers Ltd, provides a candid assessment of how private contractors navigate optimisation under increasingly rigid specifications. “In early BOT projects, we had the freedom to design with a 20 to 30-year maintenance horizon in mind. Now, most designs are fixed by the authority or DPR consultants, leaving little room for innovation,” he elaborates.
In such cases, material substitution becomes the key lever for cost optimisation. IRB has made significant strides in this direction, with extensive use of fly ash, ground granulated blast furnace slag (GGBS), steel slag, and recycled materials. “We have invested in a recycling plant capable of processing 60–70 per cent RAP (Recycled Asphalt Pavement). That’s the kind of shift that matters,” explains Dr Hoshing.
He stresses that cost optimisation does not mean lowering quality. “A road that fails in two years is a financial disaster. True savings come from building durable assets using smarter processes and materials,” he adds.
The lack of flexibility in current procurement models, especially under EPC and HAM contracts, leaves little room for contractors to apply design innovations. “While PPP contracts should ideally follow output-based specifications, in India we often default to input-based design, which constrains innovation,” opines Devayan Dey, Partner at PwC India.
Dr Hoshing advocates granting of more design latitude to concessionaires, allowing them to apply value engineering techniques. “We’re often forced to include unnecessary components like roadside call boxes that are obsolete in the smartphone era. This adds to costs without delivering value,” he says.
R K Pandey concurs, suggesting that value engineering and cost optimisation should be mandatory components of DPR preparation. “Every project proposal should include a section justifying why a particular alignment, material, or method was chosen over other alternatives,” he stresses.
Sustainable materials and the circular economy
With environmental awareness rising, there is a growing need to use industrial by-products such as steel slag, red mud, copper slag, and biochar in road construction. CRRI’s research has helped develop processing techniques and guidelines for these materials, which are now being trialled across India. Dr Parida cites the Ministry of Steel project co-developed with Tata Steel, JSW, and AMNS that enabled steel slag to be used in trial stretches in Surat and Jamshedpur. “Once these materials are standardised under IRC codes, their use can be scaled nationally,” he explains.
Dr Ramachandra adds, “Bottom ash, a by-product of thermal power plants, offers similar potential. We generate about 35–40 million tonnes annually, and up to 50 per cent of it can be used in road layers. But we need guidelines and quality checks in place.”
According to him, more composite cements and multi-blend mixes should be used in road construction, as they lower carbon footprints while improving durability.
From environmental ratings to material recycling, many construction companies have taken steps in integrating ESG principles into construction. “In the past three years, IRB Infrastructure has gone from a sustainability rating of 0.7 to 52—among the highest in the industry,” says Dr Hoshing.
Apart from material recycling, IRB has implemented water reuse systems in its hot mix plants, installed emission control systems, and designed drainage infrastructure to store and recycle water on-site. “The use of glass fibre reinforcements and steel fibres is also emerging as effective tools to reduce thickness and improve road performance,” he highlights.
Experts also feel that there is a need for continual revision of IRC and BIS codes to reflect field learnings.
Focus on right procurement and digitalisation strategies
Having right procurement strategies are often considered as the key for improving operational efficiency in road construction projects. Many firms have adopted centralised procurement for all major materials like steel and cement, which leads to bulk discounts and improved cash flow management. “There are also new models where vendors handle procurement and receive staggered payments from contractors, easing liquidity pressure. Equipment rental models with manpower bundles also help reduce capital outlay,” elaborates Dr Hoshing.
Dey suggests a three-pronged roadmap for cost optimisation in Indian road construction:
- Design innovation: Empower private players with flexibility in design, remove rigid specifications, and promote value engineering during project preparation.
- Supply chain efficiency: Promote use of recycled and alternative materials, optimise procurement models, and reduce dependency on scarce natural aggregates.
- Technology adoption: Embrace digital tools in quality control, project tracking, and asset management to boost speed, transparency, and durability.
Experts agree that the next leap in optimisation would come from digital construction. Pandey predicts a move from mechanised to autonomous construction, reducing errors and improving speed.
AI-driven field inspection—where drone footage, photo annotations, and speech-to-text interfaces help generate real-time progress reports—has the potential to cut down layers of bureaucracy and improving accountability. “Even requests for inspection and quality control tests can now be logged digitally. We are inching closer to real-time monitoring across the board,” opines Dr Hoshing.
India stands at a pivotal moment in its infrastructure journey. If innovation, sustainability, and engineering excellence are institutionalised across public and private sectors, cost-effective yet world-class roads can indeed become a reality.
Footnote:
(This article is based on the virtual panel discussion hosted by FIRST Construction Council on the topic of “Cost Optimisation in Road Construction” on May 16, 2025. This panel discussion was organised in association with Construction World, Infrastructure Today and Equipment India magazines.)

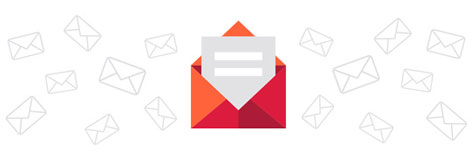
Subscribe Now
Subscribe to our Newsletter & Stay updated
RECENT POSTS
Popular Tags
Folliow us
Related Stories
“Our cutting-edge excavators are Made in India.”
How are hydraulic excavators used in different construction and mining applications?
“Our cutting-edge excavators are Made in India.”
How are hydraulic excavators used in different construction and mining applications?
Future Excavated
In India’s sweeping infrastructure transformation, hydraulic excavators have emerged as the silent powerhouses behind the scenes. Whether it’...